In today's manufacturing industry, which pursues high precision and performance, precision injection molding technology has become a focus due to its wide application in high - end fields like aerospace and electronics. Meeting the needs of precision injection molding hinges on equipment performance.
Ordinary injection molding machines typically have an injection pressure of 147 - 177MPa, while precision ones require 216 - 243MPa, and ultra - high - pressure models can reach 243 - 392MPa. Higher pressure increases product density, reduces shrinkage and deformation, and enables thinner wall thickness. The injection speed of precision hydraulic injection molding machines should exceed 200mm/s, and that of all - electric ones should be over 300mm/s to meet the short filling time of precision products and boost productivity.
The capacity deviation of the injection molding machine should be within about 20% of the product tolerance. With a displacement sensor of 0.1mm accuracy, the metering, injection stroke, and cushion thickness are precisely controlled to ensure stable injection volume and product dimensional accuracy.
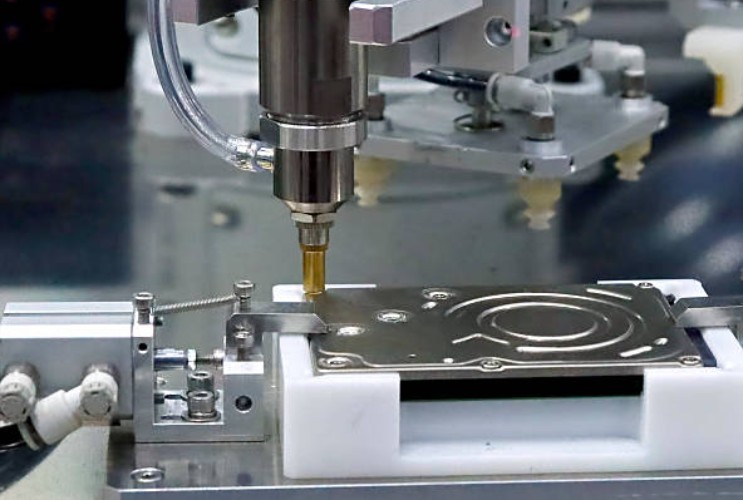
High - precision PID control is required to keep the temperature fluctuation within ±1℃, with even stricter requirements for ultra - precision injection molding. Stable temperature is crucial for plastic fluidity and formability.
Mold temperature affects product thermal shrinkage and appearance. Precision injection molding needs an accurate mold temperature control system, keeping the mold cavity surface temperature variation within ±1℃. Fuzzy control can be used for ultra - precision molding.
Oil temperature changes can disrupt injection pressure. A cooling device is needed to maintain the temperature at 50 - 55℃ for stable molding.
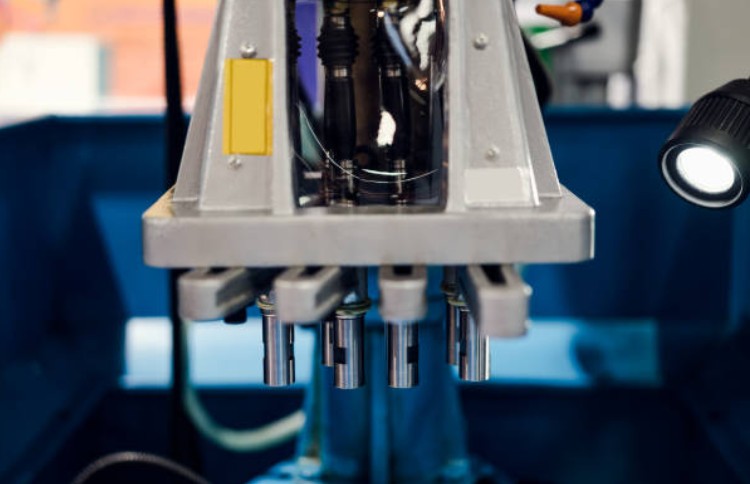
The flatness of the fixed platen should be maintained at 0.08 - 0.10mm, and the parallelism of the moving and fixed platens should be controlled within 0.08 - 0.10mm to prevent mold deformation under high pressure and ensure product accuracy and surface quality.
The clamping force should be uniform, adjustable, stable, and repeatable, with the opening accuracy controlled within 0.03mm and the closing accuracy within 0.01mm.
The opening and closing speed of the clamping mechanism is about 60mm/s, shortening the molding cycle and improving efficiency.
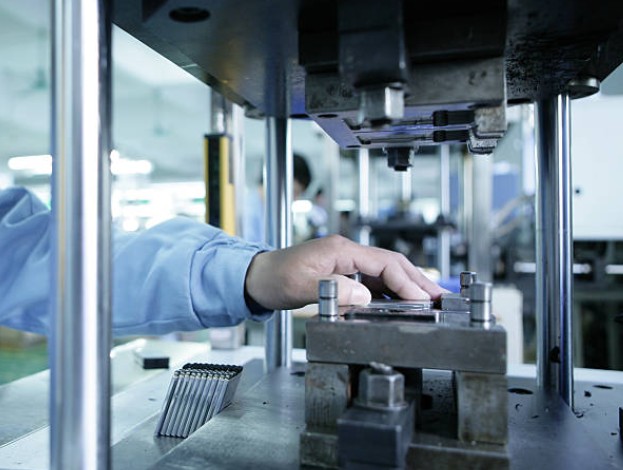
Select high - sensitivity hydraulic components, adopt cartridge proportional technology, or install servo valves or use variable - displacement pump injection molding machines to enhance system response speed and repeatability for stable and controllable molding.
Use proportional pressure valves, flow valves, or servo variable - displacement pumps for energy saving, fast pressure and flow conversion, and reduced fluctuations.
For direct - pressure injection molding machines, separate the clamping and injection oil circuits to avoid pump overload. During holding pressure, a small pump supplies oil separately to the clamping system, and a pilot - operated check valve is installed for energy saving and enhanced hydraulic rigidity.
Modern precision injection molding machines feature full computer control. The hydraulic system, controllers, and instruments work together with intelligent functions for low - noise and stable operation.
Moreover, the platens, tie bars, and frame of the equipment should have high stiffness; a high - precision low - pressure mold protection device should be equipped; sufficient mold space should be reserved for large - scale molds; and the plasticizing components should have strong plasticizing ability and wear - resistant materials. Only when all systems of the equipment meet the requirements can high - quality precision injection - molded products be produced, promoting the high - quality development of the manufacturing industry.
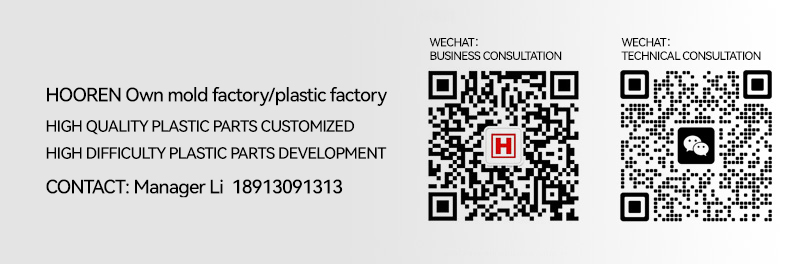