In the wave of intelligent manufacturing upgrades, the precision injection molding sector is shifting from experience-driven to data-driven operations. By integrating technologies such as the Internet of Things (IoT), artificial intelligence (AI), and digital twin, an intelligent system covering the entire production process is constructed to address traditional pain points like difficult parameter control, quality fluctuations, and limited efficiency—providing support for high-end manufacturing in medical, automotive, and electronics industries. The implementation paths are analyzed from four dimensions: intelligent perception, process optimization, flexible collaboration, and quality closed-loop.
A full-chain sensing network for injection molding machines, molds, and auxiliary equipment forms the foundation of intelligent precision injection molding:
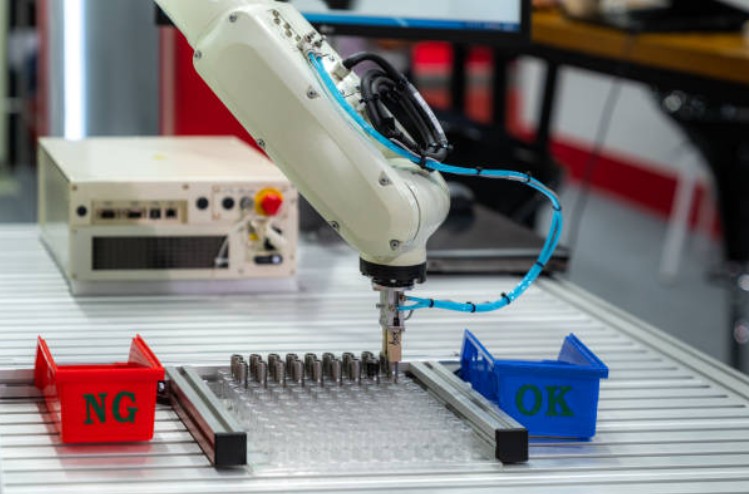
Injection Molding Machines: Industrial data acquisition gateways capture core parameters (temperature, pressure, injection speed, screw position) at 50ms-level frequency, compatible with protocols of mainstream equipment (Sumitomo, Haitian, etc.) for rapid, manual-configuration-free access and "second-level" data collection.
Molds: Sensors (pressure, hot runner temperature, strain gauges) monitor clamping force, cavity pressure, and thermal deformation. Automatic shutdown triggers when clamping force exceeds 15% of the rated value to prevent damage.
Auxiliary Equipment: Data linkage among dryers, feeding systems, and robots—e.g., real-time correlation between raw material moisture content and process parameters to compensate for material variations and ensure melt quality.
Based on OPC-UA and MQTT protocols, data links between injection molding machines, MES, and ERP are established: Edge computing modules calibrate process parameters in real time (e.g., ±1℃ melt temperature deviation), with <30ms response to avoid cloud-dependent delays; vibration and current sensors predict equipment failures, reducing average response time to within 2 hours.
A "data-decision-validation" closed loop is built via deep learning models:
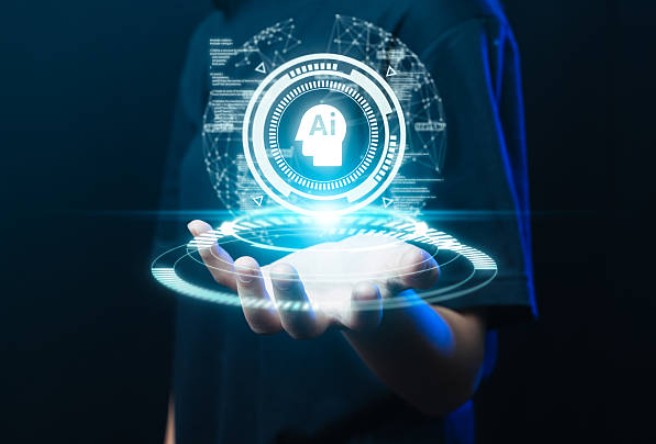
Intelligent Parameter Recommendation: Training models with millions of qualified process data sets to output optimal parameter combinations (holding time ±0.1s, injection speed ±1mm/s), increasing yield from 95% to 99.5%.
Multivariable Coupling Resolution: Balancing temperature, pressure, and time to solve filling shortages in thin-walled parts and shrinkage in thick-walled parts. For example, AI optimization reduces the molding cycle of mobile phone frames by 12% and defect rate to 0.5%.
Digital twin technology combined with physical sensors enables "health visualization" for molds: A health model integrating temperature, opening/closing cycles, and force peaks achieves 90% crack warning accuracy (e.g., automatic cooling triggers at 200℃ for 5 minutes); intelligent lubrication reduces wear by 40%, and "degraded reuse" of aged molds extends service life by 25%, saving 30% annual mold costs.
Central control systems enable flexible collaboration among injection molding machines, robots, and inspection equipment:
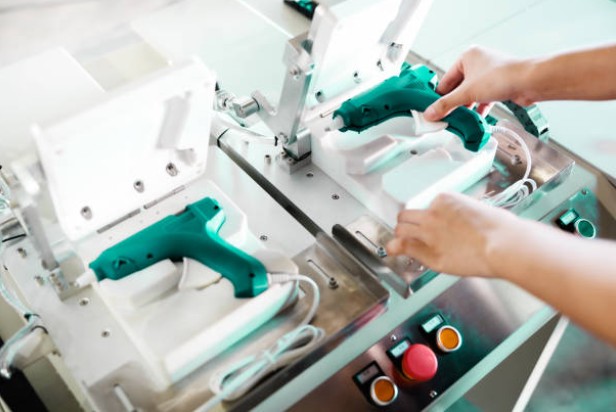
Order-Driven Changeover: For multi-variety, small-batch orders, mold parameters and process curves are automatically called (e.g., 10-second parameter matching for medical consumable molds), improving changeover efficiency by 40%.
Dynamic Capacity Allocation: Intelligent scheduling of injection molding machines based on order priority (e.g., urgent medical components) increases capacity utilization from 80% to 95%, ensuring on-time delivery.
Centralized feeding systems address raw material control pain points: Customized conveying solutions for different materials (e.g., LCP closed-loop conveying with <3mg/m3 dust and ≤0.02% moisture) eliminate defects like interior shrinkage and lens fogging; AGV feeding and robotic loading/unloading reduce manual positions by 15 per line, cutting labor costs by 30%.
A complete "product-process-equipment" data chain is established:
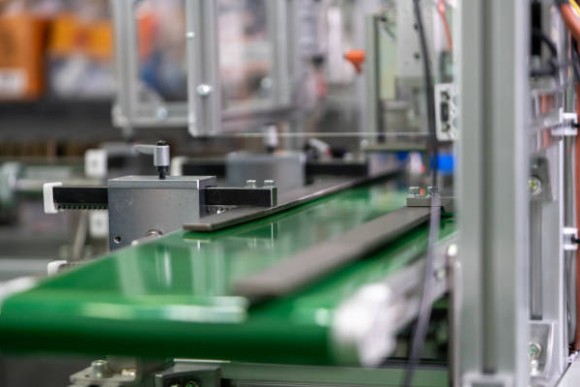
Batch-Level Traceability: Parameters from raw material drying to injection are linked to batch numbers, locating defect roots within 5 minutes for reverse tracing.
Real-Time Quality Dashboards: Multi-terminal display of key indicators (shrinkage rate, flash rate) reduces quality response time from 3 hours to 10 minutes.
Combining Statistical Process Control (SPC) with AI analysis, a quality improvement loop is formed: Clustering analysis identifies parameter correlations for defects (e.g., flash vs. mold temperature/holding time), enabling preventive measures; qualified product data iteratively optimizes process models, reducing customer return rates from 3% to 0.2%.
The three-step implementation framework includes:
Equipment digitization (1–2 weeks): Deploy data acquisition gateways for equipment and sensor integration.
Process intelligence (2–4 weeks): Train AI models with historical data to launch parameter recommendation systems.
Production line collaboration (4+ weeks): Expand modules and connect to MES/ERP for end-to-end data integration.
Driven by high-end industry demands, precision injection molding intelligence is evolving from single-point applications to full-process coverage. Future integration of digital twin and carbon footprint tracking will advance the industry toward "autonomous decision-making manufacturing," realizing high-precision, high-efficiency, and low-energy sustainable development. Embracing intelligent solutions is key to overcoming industry pain points and seizing high-end manufacturing opportunities.
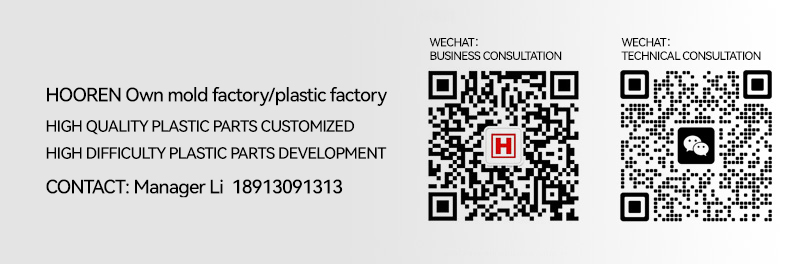