Insert injection molding is a plastic processing technology. It embeds inserts made of metal, glass, ceramics, or other materials into plastic products during the injection molding process, achieving the combination of different materials and obtaining products with specific properties and functions. Its principle is to accurately place the inserts in specific positions of the injection mold first. After closing the mold, molten plastic is injected into the mold cavity. The plastic fills the mold and wraps the inserts during the flowing process. After cooling and solidification, it firmly combines with the inserts to form an integrated body.
Insert injection molding can combine the formability and insulation of plastic with the high strength and high electrical conductivity of metal to manufacture products with excellent comprehensive properties. For example, in automotive electronic connectors, metal inserts provide electrical connection and mechanical strength, while the plastic part plays a role in insulation and protection, enabling the product to stably transmit current and prevent short circuits.
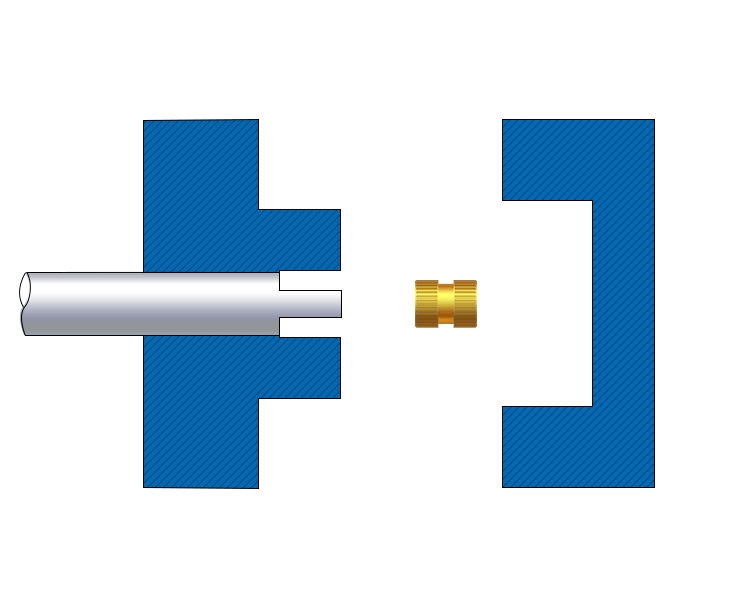
For plastic products that need to withstand large external forces or have high requirements for structural strength, the addition of inserts can significantly enhance their strength and stiffness. For instance, embedding metal rod inserts in tool handles can effectively prevent the handles from deforming or breaking during use, improving durability.
In electronic and electrical products, by embedding inserts such as metal sheets, wires, and plates, functions such as electrical conductivity and shielding can be realized. For example, embedding a metal shielding cover during the injection molding of a mobile phone shell can reduce electromagnetic interference and ensure stable signal transmission.
For some products, using the insert injection molding process can achieve the structure that originally requires the assembly of multiple components through one injection molding, reducing the assembly process and improving production efficiency. For example, the housing of some small electrical appliances and internal metal connectors can be directly formed through insert injection molding without subsequent complex assembly.
Material Selection: According to the product's usage requirements and performance needs, select appropriate insert materials, such as metals (copper, aluminum, steel, etc.), ceramics, glass, or other special materials. Among metal inserts, copper alloys have high mechanical strength and are easy to process, but their thermal expansion coefficient differs greatly from that of plastic; aluminum has a thermal expansion coefficient that is more compatible with plastic, resulting in a firm combination but relatively lower strength.
Processing and Customization: Process the selected insert materials through processes such as cutting, grinding, drilling, and stamping to make their dimensions and shapes meet the design requirements. At the same time, to enhance the bonding force between the insert and the plastic, the surface of the insert is often processed by knurling, grooving, sandblasting, etc., increasing the friction force and contact area.
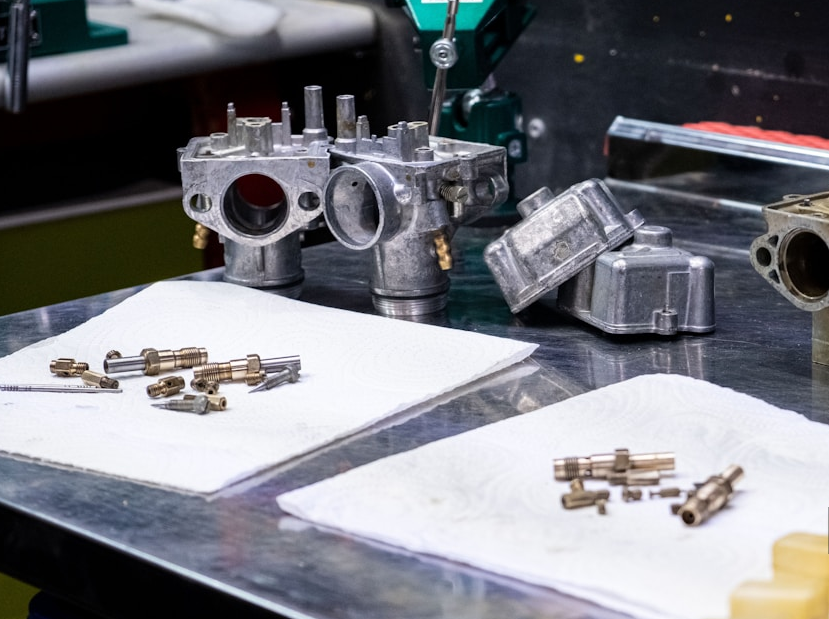
Design Key Points: The mold needs to be designed with special insert positioning and fixing devices to ensure that the inserts are accurately positioned and do not move during the injection molding process. Reasonably plan the runner system to enable the plastic melt to uniformly and smoothly fill the mold cavity and wrap the inserts, reducing molding defects such as weld lines and air pockets. In addition, the design of the cooling system is also crucial, ensuring uniform cooling of the mold and shortening the molding cycle.
Manufacturing Requirements: Use high-precision processing equipment to manufacture the mold to ensure the dimensional accuracy and surface quality of the mold. The surface roughness of the mold should meet the requirements to ensure the appearance quality of the molded product. At the same time, the strength and durability of the mold should be ensured to meet the mass production requirements.
Raw Material Preparation: According to the product's performance requirements, select appropriate plastic raw materials, such as polypropylene (PP), polyethylene (PE), polystyrene (PS), polycarbonate (PC), acrylonitrile-butadiene-styrene copolymer (ABS), etc., and carry out pre-treatment such as drying to remove moisture in the raw materials and prevent defects such as air bubbles during the molding process.
Injection Molding Parameter Setting: According to the characteristics of the plastic raw materials, the product structure, and the mold conditions, set appropriate injection molding parameters, including injection temperature, injection pressure, injection speed, holding pressure, holding time, cooling time, etc. For example, the injection temperature should ensure that the plastic is in a good molten state, and the injection pressure should be sufficient to make the plastic melt fill the mold cavity.
Injection Molding Operation: Accurately place the inserts in the predetermined positions in the mold cavity. After closing the mold, inject the molten plastic into the mold. During the injection molding process, closely monitor the operation status of the injection molding equipment and process parameters to ensure the stability of the injection molding process.
Demoulding: After the plastic has cooled and solidified to a certain extent in the mold cavity, open the mold and eject the molded product from the mold through the ejector mechanism.
Trimming: Remove burrs, flash, etc. from the product and perform preliminary treatment on the product's appearance to make its surface smooth and clean.
Inspection: According to the product quality standards, inspect the product in terms of dimensional accuracy, appearance quality, performance, etc. Check whether the combination between the insert and the plastic is firm and whether there are defects such as cracks, pores, and deformation in the product.
Packaging: Package the qualified products, select appropriate packaging materials and methods to prevent the products from being damaged during transportation and storage.
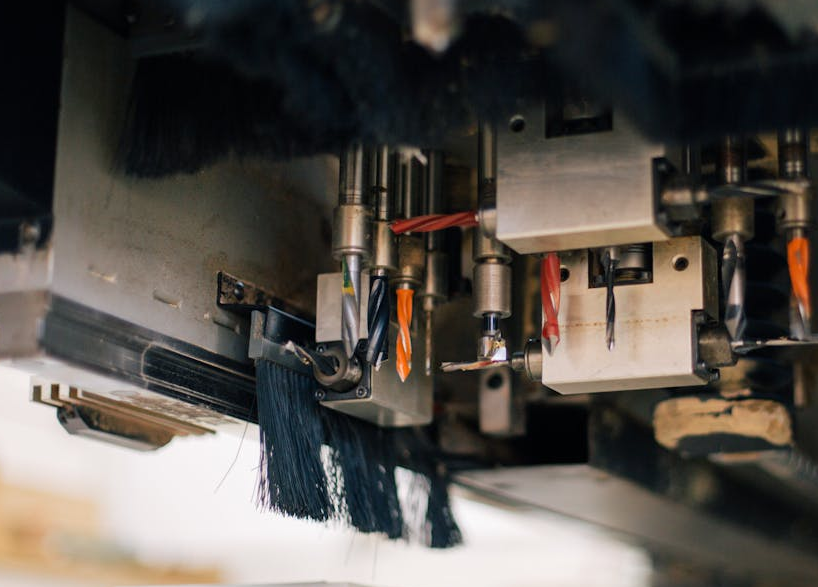
It is widely used in the casings of various electronic products, internal connectors, plug-ins, switches, sockets, etc. For example, embedding metal inserts in the casing of a laptop can enhance its structural strength and electromagnetic shielding performance; the plug part of a mobile phone charger achieves a firm combination of metal pins and the plastic shell through insert injection molding.
It is used to manufacture automotive parts, such as automotive instrument panels, door handles, steering wheels, and plastic parts around the engine. For example, metal or plastic inserts are embedded in the automotive instrument panel for installing components such as instruments and sensors, while improving the overall strength and stability of the instrument panel.
It is applied to parts such as the handles and casings of some mechanical parts. For example, in the handle of an electric tool, metal or rigid plastic inserts are embedded through insert injection molding, improving the comfort and strength of the handle, and making it easy to operate and withstand large external forces.
It is commonly found in some household daily necessities, such as the connectors of plastic furniture and the plastic parts of bathroom products. For example, the connection part between the leg and the seat surface of a plastic chair uses insert injection molding to enhance the connection strength and extend the service life.
During the injection molding process, the insert may be displaced due to inaccurate mold positioning, improper setting of injection molding parameters (such as too fast injection speed and too high pressure), etc., resulting in unqualified products. Solutions include optimizing the mold design and using more accurate positioning devices; reasonably adjusting the injection molding parameters to control the flow speed and pressure of the plastic melt.
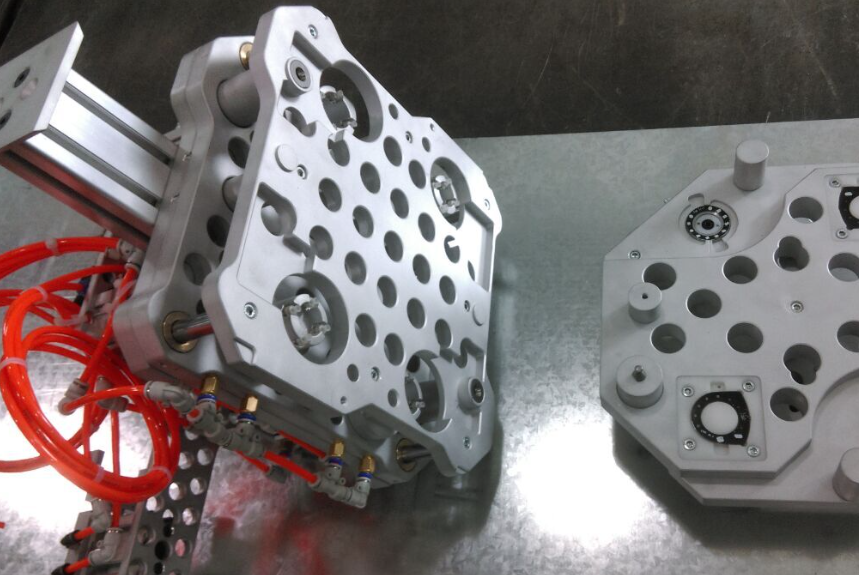
When the plastic melt encounters obstacles such as inserts during the flowing process, it diverges and then converges, easily forming weld lines, affecting the appearance and strength of the product. The mold temperature can be adjusted, the injection speed and pressure can be optimized to make the plastic melt better integrated; post-processing such as heat treatment or mechanical processing can be carried out on the product to reduce the weld line marks.
Poor exhaust of the mold or gas generated by the thermal decomposition of the plastic will form air pockets inside the product, affecting the product quality. It is necessary to ensure the smoothness of the mold exhaust system, reasonably design the exhaust slots; optimize the injection molding parameters to make the plastic melt smoothly discharge the gas during the filling process. If necessary, vacuum-assisted molding technology can be used.
The weak bonding between the insert and the plastic may be due to improper surface treatment of the insert, poor compatibility between the plastic and the insert material, etc. The surface treatment process of the insert can be improved, appropriate plastic raw materials and additives can be selected to improve the bonding performance between them.
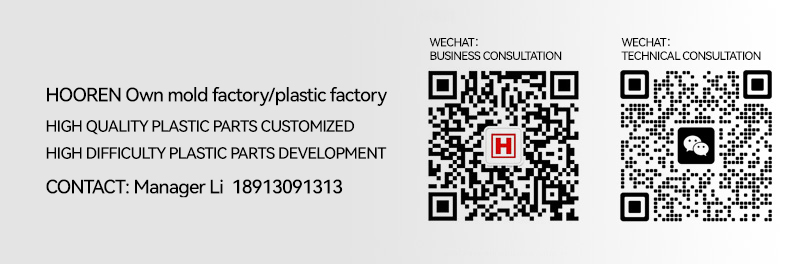